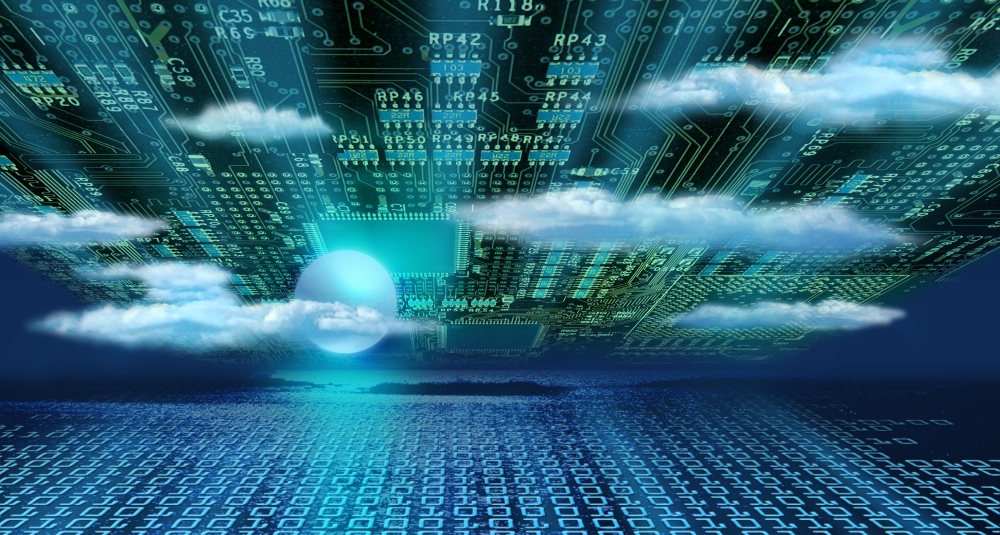
The digitization of processes that drives competition in today’s global markets is nowhere more evident than on the plant floor.
Across the world, the traditional manufacturing industry is in the throes of a widespread digital transformation that is accelerated by exponentially growing technologies such as intelligent robots, smart sensors, additive manufacturing, and machine learning.
They have completely changed how people interact with equipment and how products are designed and manufactured.
According to Kepware, 9 out of 10 industrial companies are already on their digital transformation journey - and rightly so driven by their inherent benefits and the downright necessity for competitive sustainability.
However, they are often faced with a double-edged sword. While digital transformation promises a high return on investment with the proper execution, the transition process comes with high upfront costs and is far from smooth sailing.
Below, we discuss a few common challenges that can or could plague anyone going through that transformation journey.
Cost
The downstream benefits of digital transformation often come with quite hefty upfront costs. The scope of cost savings that digital transformation can introduce is wide-ranging and unique to each organization and industry.
While the goal is to maximize the ROI from the digital transformation, it is important to be aware of the following costs and plan for them:
- Technology and Infrastructure: These are the hard costs associated with procuring, installing, commissioning, and integrating the new technology and infrastructure. In most cases, these costs will form the largest portion of your overall cost but are also typically easier to estimate. However, one of the pitfalls is running into scope creep due to discovery issues during field execution, especially if the work is being done in an old plant with older equipment and infrastructure.
- Systems and Processes: As you install new technology, you will likely need to start doing things in new ways, from how your supply chain team orders new inventory to the maintenance procedures and documentation on the plant floor. Often, this cost is the hardest to estimate since it cannot be based on the cost and quotes of tangible equipment and assets - so, you may benefit from allocating a larger contingency cost float to this.
- Human Capital Expenditures: This generally includes two main components - the cost associated with personnel training and the overall cost of organizational buy-in. The training costs will typically come in the form of the new technical, operational, and maintenance knowledge required on the plant floor associated with the new technology, systems, and processes. The cost of organizational buy-in does not often appear front and center and is the hidden cost often associated with the effort and uphill battle required to initiate and execute the transformation.
There are many factors surrounding digital transformation that are impossible to know precisely at the outset. As a result, many initiatives fail because leaders often develop too rigid and too detailed budget plans before really understanding the realities of the adjustments that may be necessary over time in a multi-year digital transformation.
Instead of having a rigid plan upfront, it may be better off to break projects down into a series of gates (or milestones), which are phases that the company will go through as the digital transformation journey evolves. This would involve developing a detailed plan and budget only for the upcoming gate. Each gate is also a goal, through which leadership teams will build confidence and commitment towards the next new gate.
The key to success is recognizing that digital transformation is a multi-year journey, and leaders will find it difficult to predict the obstacles. However, despite the many unknown factors that may be present at the outset - you can manage the risks by funding the transformation flexibly, gate by gate.
Data Management
Equipment operating data (such as machine run hours and process parameters) form the backbone of a plant’s predictive maintenance (PdM) and condition-based maintenance (CBM) programs.
CBMs and PDMs are now the primary strategies in asset management as most manufacturers have shifted away from fixed-interval preventive maintenance methods. One of the key challenges faced by most is managing this data stream from its distributed asset fleet and ensuring that it is accessible, usable, and reliable.
For example, one of the many ways this can be facilitated is by embedding MQTT protocols within the plant’s programmable logic controllers (PLCs). This enables secure data exchange between the distributed equipment on the plant floor and cloud data warehouses hosted by Microsoft Azure, IBM (News - Alert) Cloud, Amazon Web Services, Google Cloud Platform, SAP Cloud, and others.
Such solutions bring location-independent data visualization capabilities through the Enterprise Asset Management (EAM) platforms that help provide an enterprise-level view to company leaders while giving users full authority over their proprietary data.
Data Security
As digitization enables users to view their plant systems remotely from anywhere globally, it also means those systems need to be protected accordingly. This is the other aspect of the challenge associated with digital assets.
With the progression onto smart factories and the Internet of Things (IoT), these threats now work on an entirely new level and can result in serious physical and business consequences. Data and cybersecurity breaches can have varying levels of impact. For example, the Colonial Pipeline ransomware attack in the US this year sparked a country-wide temporary shortage of gasoline.
Some common data and cybersecurity risk vulnerabilities arise from:
- Every connected device poses a potential security risk of cyber attack
- IoT now connects previously isolated systems and equipment, which increases the attack surface
- System upgrades are often installed piecemeal given their increasing complexity and may not incorporate the incremental required security measures
Most regional governments and regulators have recommendations in place for industrial security and employ a defense-in-depth strategy of a multi-layered protection system.
Some technical examples of data security measures implemented in most places may involve data encryption before transferring it to the cloud over VPN connections or having an onboard firewall.
Additionally, companies should conduct a detailed data and cybersecurity audit to evaluate the robustness of existing security protocols, requirements, and governance. This would typically involve identifying the most critical information assets to protect, map how the information flows through them, assess their vulnerabilities through breach and attack simulation (BAS), and determine the risk associated with if that information was lost or compromised.
A detailed audit such as this will enable companies to protect the equipment on the floor by taking appropriate and targeted action based on risk tolerance.
Change Management
Change management is the glue that holds together the digital transformation process. It’s multifaceted in nature and is essential in managing the aforementioned challenges. The two broad areas of change management that apply to most digital transformation initiatives include:
- Engineering change management: This is more on the technical side of ensuring the design and operation of the plant undergoes a controlled change process both on paper and in the field.
- Organizational change management: Successful digital transformation needs robust organization change management, where it is incumbent upon the leaders to understand the complexities of the organization's culture and structure. Often, it is the mental barrier of the working-level employees that constitutes the main challenge to digital innovation.
Engineering change management is a more objective form of change management, and each company or industry would usually have its own standards, regulations, and protocols around engineering change control.
Some of the common best practices in successfully navigating engineering change management are:
- onboarding subject matter experts
- having a robust verification and review process
- and maintaining a transparent vendor quality and audit program
In terms of organizational change management, the framework around that is a bit more subjective and flexible, understanding the complexity and uniqueness of each company, the industry, and demographics.
Universally speaking, organizational change management triggered by digital transformation must involve all departments and employees at all levels - from C-Suite to plant floor level workers. Change is impossible without broader and representative employee participation, without which it may lead to growing resistance to change and create operational risks.
Employees must see the value in the transformation, feel empowered to contribute to its direction, and see how the solution is implemented.
Proper communication during organizational change is another underlying factor that determines the success or failure of a transition. Consistent and open communication keeps everyone on the same page and provides assurance to the individuals who may feel the brunt of these changes - mostly those on the plant floor.